Silicon Carbide: The Revolutionary Material Transforming Military Armor and Bulletproof Protection
- sktacticalarmour
- 2 hours ago
- 2 min read
Introduction
The evolution of modern warfare demands armor systems that reconcile protection with mobility—a challenge Silicon Carbide addresses decisively. Unlike steel or earlier ceramics, SiC’s unique properties allow it to neutralize high-velocity projectiles while minimizing weight penalties. Its covalent atomic structure enables exceptional energy dissipation, making it indispensable for personal body armor, vehicle protection, and aerospace applications. Beyond performance, SiC’s durability reduces lifecycle costs, justifying its adoption despite higher initial expenses.
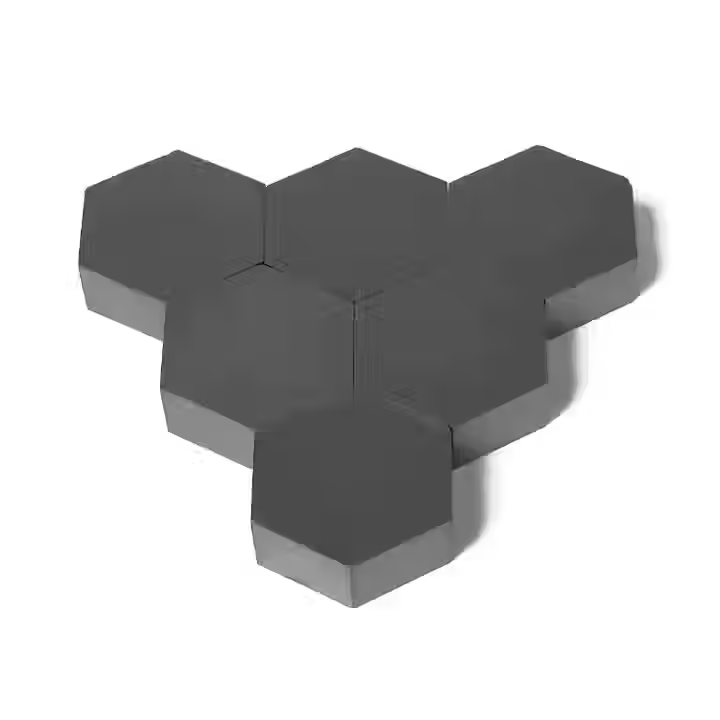
Historical Development and Material Properties
Silicon Carbide’s military journey began with its 1891 discovery by Edward Acheson, but its potential for armor was only realized during Cold War materials research. Advances in sintering and reaction bonding during the late 20th century enabled the production of complex, large-scale components.
SiC’s effectiveness stems from its atomic lattice: silicon and carbon atoms form tetrahedral bonds, yielding a material with a Mohs hardness of 13 (surpassed only by diamond and boron carbide) and a density of 3.21 g/cm³—40% lighter than steel. Its thermal conductivity (120 W/m·K) and low thermal expansion ensure stability under extreme conditions, while fracture toughness (6.8 MPa·m^0.5) prevents catastrophic failure upon impact.
Ballistically, SiC shatters incoming projectiles while distributing force across backing materials like UHMWPE. This multi-stage energy absorption outperforms monolithic materials, particularly against armor-piercing rounds.
Manufacturing and Military Applications
Producing military-grade SiC involves synthesizing high-purity powder via the Acheson process, followed by precision sintering. Pressureless sintering (2000–2200°C) creates intricate shapes, while hot pressing (1900–2000°C under 20–40 MPa pressure) optimizes density for critical armor plates. Reaction bonding, which infiltrates silicon into porous SiC preforms, is ideal for large vehicle panels.
These methods underpin SiC’s battlefield roles:
Body Armor: SAPI plates combine SiC strike faces with polyethylene backings, achieving NIJ Level IV protection at half the weight of steel. Their multi-hit capability is vital for prolonged engagements.
Vehicle Armor: Modular SiC systems protect against kinetic and shaped-charge threats while preserving mobility. Reaction-bonded panels excel here due to their thermal shock resistance.
Aerospace/Naval Use: Helicopters and ships benefit from SiC’s corrosion resistance and strength-to-weight ratio, enabling protection without compromising performance.
Comparative Advantages and Future Directions
SiC’s dominance over alternatives is clear:
Steel: SiC matches protection at 40% the weight and resists corrosion.
Alumina Ceramics: Cheaper but inferior against armor-piercing threats.
Boron Carbide: Harder but more brittle and costly to produce.
Future innovations include additive manufacturing for complex geometries, nanostructured SiC to enhance toughness, and hybrid systems integrating smart materials. Cost reduction through scaled production remains a priority to broaden deployment.
Conclusion
Silicon Carbide represents a paradigm shift in armor technology. Its physicochemical properties, manufacturing scalability, and proven performance in combat solidify its role as the material of choice for 21st-century military protection. As threats evolve, SiC’s adaptability—through advanced composites or integrated sensors—will ensure its continued relevance, safeguarding personnel and platforms while maintaining strategic mobility.
Comments